
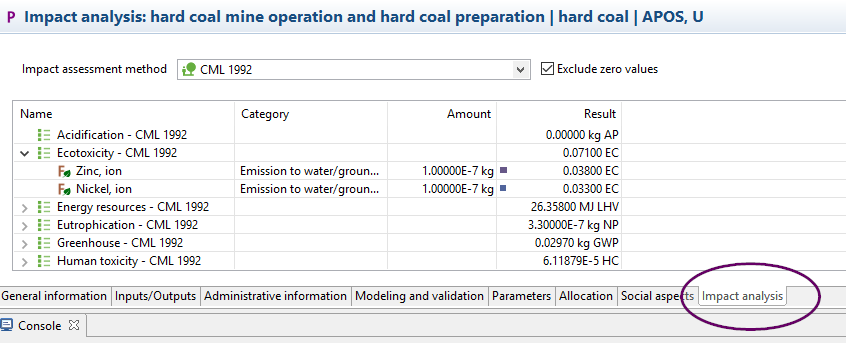
A myriad of product carbon footprints (PCFs) for specific products have been made public – from desktop computer displays 15 to formula milk 16, from cars 17 to carbon capture and storage equipment 18, or indeed sections of a company's entire portfolio of products 19 – and extensive LCA databases such as Ecoinvent® 13, GABI 20, and similar repositories have long been commercially available which store the carbon emissions (along with many other environmental impacts) of a wide range of materials (e.g., primary aluminum), energy types (e.g., electricity from photovoltaic farms), and processes (e.g., transportation by freight train). Product carbon footprinting has enjoyed increasing use, due to standardized how-to guidance and improvements in the underlying methodology 5, 10, 11, 12, 13 as well as the increased urgency to curb global carbon emissions 14.
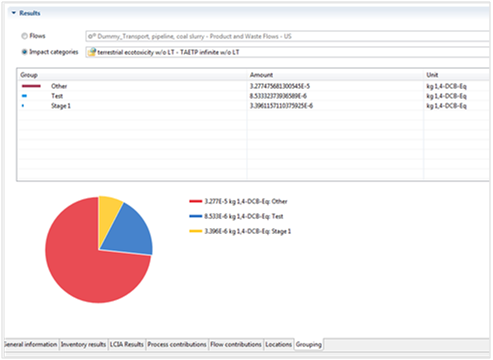
Here, and henceforth in this study, “carbon” refers collectively to the 6 commonly recognized greenhouse gases, which are aggregated into a single emission figure according to their relative global warming potentials ( Methods). It can also be thought of as a limited LCA 9 that quantifies a product’s life cycle climate change impact, but not other sustainability impacts found in wider LCA ( Discussion) 4, 7. The quantification of a product’s life cycle carbon emissions, also referred to as product carbon footprinting 7, is a specific form of several carbon accounting methods 8. Of particular interest are portions of a product’s life cycle that are outside a company’s direct operations, namely the supply chain of raw materials “upstream” of the company’s own manufacturing sites and “downstream” processes such as consumer use: While these processes may be considered as being less subject to a company’s control 5, they are often responsible for major portions of a product’s overall environmental impact and hence considered crucial levers in a company’s sustainability efforts 6. Indeed, LCA cannot only quantify a product’s current impacts, but one of the many intended purposes of LCA is to guide the (re-)design of products (including sourcing materials and the product’s production process, transportation, use, and end-of-life treatment) to render them more environmentally sustainable 4. Since its debut in Europe and the US in the late 1960s, life cycle assessment (LCA) 1, 2 has been used for quantifying the environmental impacts caused throughout the life cycle of products, including industrial, commercial, and consumer products 3. We conclude that a sector-level understanding of emissions, absent of individual PCFs, is insufficient to reliably quantify carbon emissions, and that higher reported emission reductions go hand in hand with more granular PCFs. Reported achievements to reduce emissions varied depending on whether a company had reported a PCF’s breakdown to life cycle stages or only the total emissions (10.9% average reduction with breakdown versus 3.7% without).

Across their lifecycle, the 866 products caused average total emissions of 6 times their own weight, with large variation within and across industries. This breakdown varies strongly by industry. For the 866 products, on average 45% of total value chain emissions arise upstream in the supply chain, 23% during the company’s direct operations, and 32% downstream. We used this database to elucidate the breakdown of embodied carbon emissions across products’ value chains, how this breakdown varies by industry, and whether the reported emission reductions vary with the granularity of the PCF. We have used data reported by companies to CDP for public disclosure to build a database of 866 product carbon footprints (PCFs), from 145 companies, 30 industries, and 28 countries. Life cycle-based analyses are considered crucial for designing product value chains towards lower carbon emissions.
