
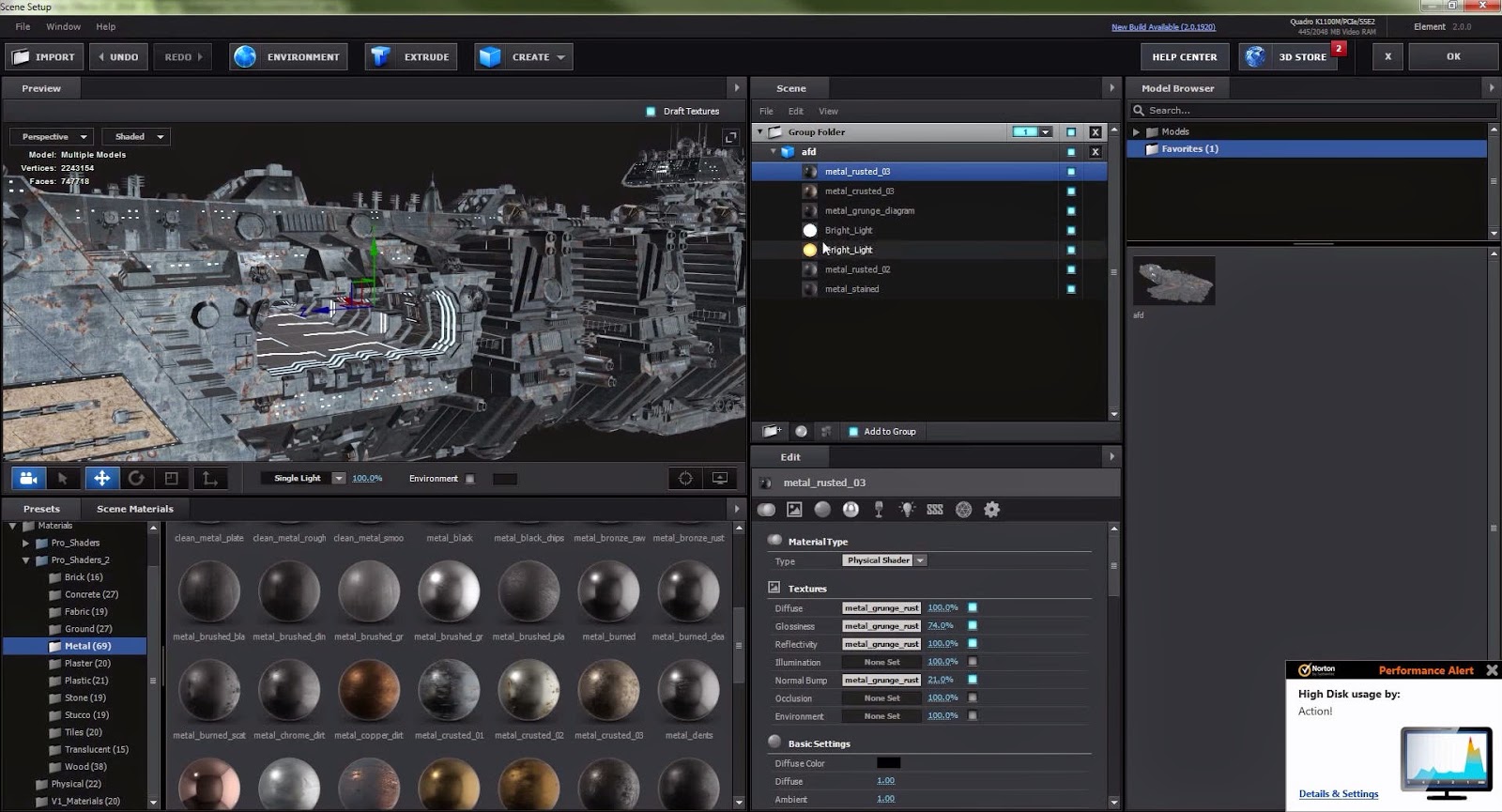
Higher energy waste streams, such as automobile engine exhaust, have larger temperature differences and yield higher conversion efficiencies. The conversion efficiencies will be too low to provide adequate payback (e.g., three years) for the thermoelectrics, associated heat exchangers and other hardware. Since thermoelectric efficiency is a function of temperature difference, most low-grade waste heat applications, at temperatures below 200☌, are not good candidates for waste heat recovery. Not all waste heat streams are good candidates for thermoelectric waste heat recovery. As researchers attempt to address this task, TE conversion continues to emerge as a prime candidate for waste heat recovery applications. Waste heat recovery recaptures this lost heat for conversion into electrical power. The American manufacturing industry as a whole does a better job of utilizing energy, but still roughly one-third of the energy consumed escapes as heat to the atmosphere or to cooling systems. Thermal cycles can be driven aggressively by compact TEC designs.Ī typical automobile converts about one-quarter of the combusted fuel energy to useful work, while the remaining energy escapes as waste heat through the radiator and engine exhaust. This feature is important for thermal cycling, or when seasonal temperature changes require dual functionality.

While vapor-compression systems can only cool, TEC systems can seamlessly switch between heating and cooling. Such extreme stability is difficult to achieve by other means. In relatively stable thermal environments, TECs achieve 0.01☌ temperature stability. The low thermal mass and fast response time of TECs, combined with an appropriate control loop, provides precise temperature control. Innovative high-watt density designs can match the cooling capacity of several such standard modules in a single (40mm) 2 module. Common designs can pump about 30 W across a 30☌ DT at a COP near. When DT can be kept low, TECs can pump heat with a COP near or exceeding. COP is low when a TEC is operated near its maximum °T, but this can be acceptable when the heat load is small. For a hot side around room temperature, temperature differences of about 72☌ and 125☌ can be achieved by single-stage and multi-stage TECs, respectively. In these cases, the combination of TE cooling and thermal insulation produces large temperature differences. In many situations, the object being cooled generates little or no heat. Based on these advantages, TEMs have come to dominate certain applications, and new benefits continue to emerge.įive primary uses of TEMs underlie these countless applications. These advantages include high reliability potential, noise-free operation, vibration-free operation, scalability, orientation-independence and compactness (high energy density). As solid-state energy converters, TE modules (TEMs) have several advantages over competing technologies.
